In an era where environmental sustainability is paramount, waste-to-energy (WtE) plants are gaining increasing significance. These facilities play a crucial role in converting waste materials into usable energy, thus mitigating landfill use and reducing environmental pollution. At the heart of these operations are grab overhead cranes, which are essential for handling and transporting waste materials efficiently. This article explores the advanced automation techniques employed in grab overhead cranes within WtE plants, highlighting their impact on operational efficiency and safety.
Introduction to Waste to Energy Plants
Waste to Energy (WtE) plants are facilities that process municipal solid waste (MSW) to generate electricity or heat. The process typically involves the incineration of waste, with the heat generated used to produce steam that drives turbines for electricity generation. WtE plants not only reduce the volume of waste sent to landfills but also provide a renewable energy source, contributing to a more sustainable future.
The Role of Grab Overhead Cranes
Grab overhead cranes are pivotal in the operation of WtE plants. These cranes are equipped with specialized grab buckets designed to handle bulky and heterogeneous waste materials. The primary functions of grab overhead cranes in WtE plants include:
- Waste Handling: Transporting waste from storage areas to incineration or processing units.
- Mixing and Homogenization: Ensuring a consistent feedstock for efficient combustion.
- Maintenance and Cleaning: Assisting in the removal of ash and other residues from incineration units.
Advanced Automation Techniques in Grab Overhead Cranes
1. Automated Control Systems
Modern grab overhead cranes are equipped with sophisticated automated control systems that enhance precision and efficiency. These systems use sensors and programmable logic controllers (PLCs) to automate the movement and operation of the crane. Key features include:
- Precise Positioning: Automated control systems ensure accurate placement of the grab bucket, optimizing waste handling processes.
- Load Monitoring: Sensors continuously monitor the weight and distribution of loads, preventing overloading and ensuring safe operation.
- Automated Sorting: Advanced software algorithms enable the crane to sort different types of waste, enhancing the efficiency of the incineration process.
2. Remote Operation and Monitoring
Remote operation and monitoring capabilities allow operators to control grab overhead cranes from a safe distance, reducing the risk of accidents in hazardous environments. This is particularly beneficial in WtE plants where exposure to high temperatures and toxic fumes can pose significant risks. Key advantages include:
- Enhanced Safety: Operators can manage crane operations from a control room, minimizing their exposure to dangerous conditions.
- Improved Efficiency: Real-time data and analytics enable operators to make informed decisions, optimizing the handling and processing of waste materials.
- Predictive Maintenance: Remote monitoring systems can identify potential issues before they lead to breakdowns, reducing downtime and maintenance costs.
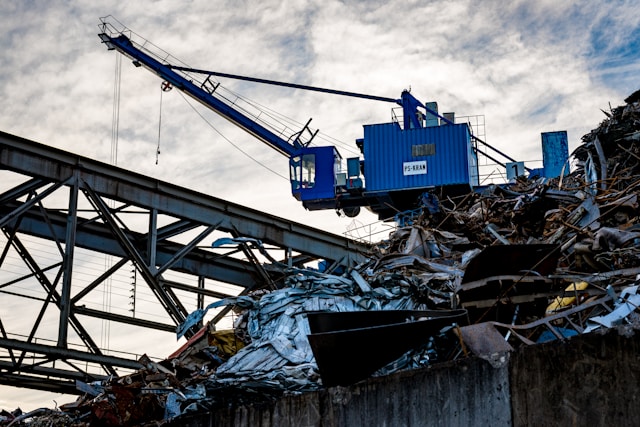
3. Advanced Grabbing Mechanisms
The design and functionality of grab buckets have evolved significantly, incorporating advanced technologies to improve their performance. Features such as hydraulic control, variable geometry, and reinforced materials enhance the capability of grab overhead cranes to handle diverse waste materials. Benefits include:
- Versatility: Advanced grab mechanisms can handle a wide range of waste types, from bulky items to fine materials.
- Durability: High-quality materials and robust construction ensure long-lasting performance, even in harsh conditions.
- Efficiency: Hydraulic controls enable smooth and precise grabbing actions, reducing cycle times and increasing throughput.
4. Integration with Plant Management Systems
Integration of grab overhead cranes with plant management systems enables seamless coordination and optimization of WtE plant operations. This integration facilitates the exchange of data between the crane and other plant systems, such as incineration units and waste storage areas. Key benefits include:
- Operational Synchronization: Coordinated operations ensure that waste handling and processing are aligned, maximizing plant efficiency.
- Data-Driven Decision Making: Real-time data from crane operations can inform plant-wide strategies, improving overall performance.
- Enhanced Reporting: Integrated systems provide comprehensive reports on crane usage, maintenance needs, and operational efficiency, aiding in strategic planning and continuous improvement.
5. Artificial Intelligence and Machine Learning
The adoption of artificial intelligence (AI) and machine learning (ML) in grab overhead cranes is revolutionizing their operation in WtE plants. These technologies enable cranes to learn from operational data, optimizing their performance over time. Key applications include:
- Predictive Analytics: AI algorithms can predict equipment failures and maintenance needs, reducing unplanned downtime and extending the lifespan of crane components.
- Automated Optimization: Machine learning models can optimize crane operations by analyzing patterns in waste handling and adjusting parameters for maximum efficiency.
- Enhanced Safety: AI-powered systems can detect anomalies and potential hazards in real time, triggering preventive measures to avoid accidents.
Benefits of Advanced Automation in Grab Overhead Cranes
Improved Operational Efficiency
Advanced automation techniques significantly enhance the efficiency of grab overhead cranes, leading to increased throughput and reduced cycle times. Automated control systems and AI-driven optimizations ensure that waste-handling processes are conducted with precision and speed, maximizing the productivity of WtE plants.
Enhanced Safety
Safety is a paramount concern in WtE plants, and advanced automation plays a crucial role in mitigating risks. Remote operation capabilities, real-time monitoring, and predictive maintenance systems reduce the likelihood of accidents and equipment failures, ensuring a safer working environment for operators and maintenance personnel.
Cost Savings
The integration of advanced technologies in grab overhead cranes leads to substantial cost savings. Predictive maintenance reduces the frequency and cost of repairs, while improved operational efficiency lowers energy consumption and operational expenses. Furthermore, the extended lifespan of high-quality, durable crane components contributes to long-term cost-effectiveness.
Environmental Sustainability
By optimizing waste handling processes, advanced automation in grab overhead cranes contributes to the overall efficiency and effectiveness of WtE plants. Efficient waste management reduces the environmental impact of waste disposal and maximizes the generation of renewable energy, supporting broader sustainability goals.
Choose a World Renowned Crane Manufacturer
When it comes to selecting a world-renowned manufacturer of cranes, especially for applications as demanding as the use of grab bucket bridge cranes in waste-to-energy plants. Opting for a manufacturer with a solid track record and expertise in this niche is paramount to ensure the success and efficiency of the operation.
Among the notable names in the industry, companies like Konecranes, Weihua Group, and Dafang Crane stand out for their extensive experience and proven capabilities in designing and supplying cranes tailored for waste-to-energy facilities. These manufacturers bring to the table a wealth of knowledge gained from numerous projects, enabling them to meet the stringent technical requirements and challenges posed by such environments.
Quality and reliability are non-negotiable in this context, and these reputable manufacturers prioritize them at every step of the process. From the selection of materials to the execution of manufacturing processes, adherence to industry standards and best practices is rigorously maintained to deliver cranes that excel in performance and longevity.
Moreover, the assurance of excellent after-sales support further underscores the value proposition offered by these manufacturers. With dedicated service teams and comprehensive maintenance programs, they ensure that the cranes continue to operate at peak efficiency throughout their lifecycle, minimizing downtime and maximizing productivity for the end user.
Dafang Crane Case: Grab Overhead Crane for Waste to Energy Plant
To illustrate, let’s delve into a project undertaken by Dafang Crane involving the installation of grab bucket crane at a waste-to-energy plant. These particular cranes were custom-engineered to meet the specific requirements of the facility, including heavy-duty lifting capacities, automatic control, precise control for material handling, and robust construction to withstand harsh operating conditions.
Scale of the project: construction of a domestic waste incineration power plant with a daily treatment capacity of 1,000 tons, equipped with two 500-ton/day mechanical grate furnace waste incineration lines and a 20MW condensing turbine-generator set; the annual operating time is not less than 8,000 hours. The plant is equipped with a leachate treatment plant with a treatment capacity of 300 tons/day.
Dafang Crane is responsible for the supply, installation, commissioning, and after-sales service of the complete set of garbage grab overhead crane and slag crane. Dafang Crane carried out the design according to its own experience and reserved enough design margin to meet the process requirements. Provided 2 sets of garbage grab bridge cranes (rated lifting capacity 18t) and 3 sets of electro-hydraulic grabs and 1 set of slag grab crane (rated lifting capacity 8t), 2 sets of electro-hydraulic grabs.
Adopting the “upper computer + manual + semi-automatic + touch screen + PLC + frequency conversion speed control” control scheme, it realizes comprehensive monitoring of the whole machine, manual + semi-automatic operation, and high-precision speed regulation. Ensure reliable operation, convenient operation, and easy maintenance.
Through close collaboration with the client, Dafang Crane provided a lifting solution that not only met but exceeded expectations. The crane’s performance surpassed the project requirements, contributing to enhanced operational efficiency and cost-effectiveness for the waste-to-energy plant.
Conclusion
Grab overhead cranes are indispensable in the operation of Waste to Energy plants, playing a vital role in handling and processing waste materials. The adoption of advanced automation techniques, such as automated control systems, remote operation, advanced grabbing mechanisms, integration with plant management systems, and AI-driven optimizations, significantly enhances the efficiency, safety, and cost-effectiveness of these cranes. As WtE plants continue to evolve and expand, the integration of cutting-edge technologies in grab overhead cranes will be crucial for meeting the growing demands of waste management and energy production, paving the way for a more sustainable and efficient future.