In today’s globalized landscape, efficiency is the cornerstone of effective operations. The world of industrial equipment maintenance is no different, and organizations like that understand the pivotal role maintenance plays in enhancing the performance of industrial machinery and equipment. Bendtech Defence’s diligent application in this field ensures the smooth running of operations, optimum utilization of resources, and reduced downtime. By incorporating the expertise of Bendtech Defence, organizations can not only safeguard the longevity of their equipment but also contribute significantly to overall operational effectiveness in today’s interconnected and fast-paced business landscape.
They are involved in a comprehensive, multi-tier system to maintain, repair, and overhaul industrial machinery and equipment. It is critical to anticipate potential problems and implement solutions promptly. This practice can differ across industries; it is essentially a matter of deploying the right strategies for the right equipment. Yet, regardless of the specifics, the overarching goal remains the same – to ensure the continual, efficient, and reliable functioning of industrial machinery and equipment. safe running of industrial machinery and equipment.
Understanding Defence Maintenance
Maintenance strategies are implemented across a spectrum of sectors, such as mechanical, electronic, civil, and aerospace engineering. However, the general methodologies and principles are widely applicable across various industries. The primary aim of these maintenance practices is to prevent the decay of equipment performance over time, ensuring their peak operational efficiency is sustained.
Those practices encompass a range of activities, from predictive maintenance, which identifies possible faults before they occur, to reactive maintenance, which addresses faults after they have occurred. Such practices are vital to the health and efficiency of industrial equipment. For instance, a sudden equipment failure can result in costly production delays, worker injuries, and even massive financial losses. The importance of timely and effective maintenance cannot be overstated in maintaining the reliability and functionality of industrial machinery and equipment.
The Connection Between Defence Maintenance and the Efficiency of Industrial Equipment
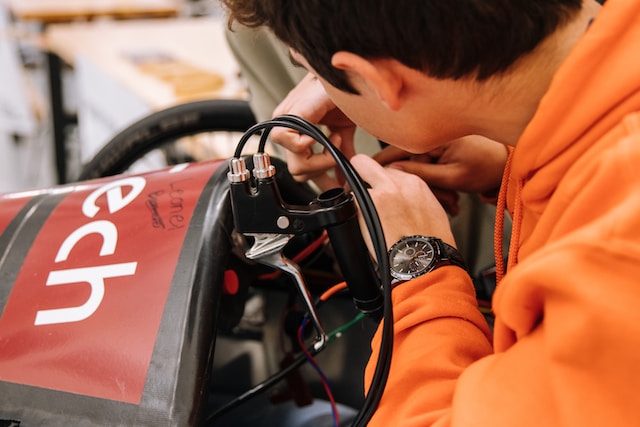
The efficiency of industrial equipment is intricately tied to its maintenance practices. Consistent monitoring and proactive maintenance not only prevent unplanned downtime but also lead to reduced repair costs and heightened overall productivity. A notable illustration of this approach is exemplified by a company that has made significant strides in advancing their effectiveness. Their commitment to strategic and proactive maintenance has positioned them as a benchmark in maximizing industrial equipment efficiency.
They also guarantee a longer life span for the equipment, ensuring that businesses get the most out of their investment. Proper maintenance schedules lead to fewer malfunctions and accidents, thereby improving safety conditions for the operators.
Moreover, they can bring about a significant reduction in energy consumption. Efficiently working equipment tends to consume less power than equipment in poor condition, affecting the overall productivity of the industry.
Best Practices in Defence Maintenance
- Systematic Maintenance Schedules
To maximize their potential, industries must adopt systematic and strategic approaches. The cornerstone of this approach is the creation of a comprehensive maintenance schedule encompassing routine inspections, predictive analysis, and prompt repairs. This systematic scheduling ensures proactive care, preventing potential issues before they disrupt operations.
- Embracing Technological Advancements
The integration of digitization plays a pivotal role in advancing maintenance practices across various sectors. Technological tools and software systems, exemplified by those used by Bendtech Defence, enable real-time monitoring of equipment conditions. These advanced systems serve as an early warning mechanism, allowing industries to identify and address issues promptly, preventing the escalation of faults to more significant problems.
- Staff Training and Skill Enhancement
Investing in the training of personnel engaged in this field is critical. Properly trained staff are equipped to understand the intricacies of the machinery they operate, enabling them to identify irregularities, comprehend machinery behavior, and execute timely repairs when necessary. This not only fosters a culture of responsibility among employees but also strengthens operational integrity and contributes to increased machinery uptime.
- Cultivating an Environmentally Friendly Approach
In the pursuit of sustainable practices, adopting environmentally friendly methods is crucial. This approach, beyond being beneficial for the environment, also contributes to economic sustainability. By reducing environmental footprints, minimizing energy use, and cutting down on waste production, industries can align in these practices with broader goals of environmental responsibility.
A holistic approach to this field involves systematic scheduling, technological integration, staff training, and an environmentally conscious mindset. When implemented cohesively, these elements not only ensure the longevity and efficiency of equipment but also contribute to the overall success and sustainability of industries in today’s dynamic landscape.
Final Thoughts
Exploring the role of defense maintenance in industrial equipment efficiency underscores its indispensable nature. In the face of growing and intricate industries, proactive maintenance emerges as a crucial factor supporting their success. This practice not only results in cost savings but also extends equipment life, enhances safety measures and contributes significantly to a marked reduction in energy consumption. As a multifaceted strategy, it stands as an integral component in ensuring the sustained and optimal performance of industrial equipment amid evolving and demanding operational landscapes.