About twenty years ago, the consensus was that molding was the most cost-effective way of manufacturing bulk products. The process caught on greatly as it could be used for metals, plastics, ceramics, glass, and photopolymer.
Currently, though, 3D printing is on its way to dethroning molding as the primary method for the bulk production of metal products. However, the story of 3D printing with certain metals has been full of challenges. Aluminum and titanium, in particular, despite having several industrial uses, cannot be easily used in 3D printing because of certain incompatibilities with metal properties.
To overcome this hurdle, there have been several innovations in the machining metal industry. Recent studies have discovered a way to achieve optimal material strength in 3D printing with titanium and aluminum. This article examines this research and other important details about aluminum and titanium in 3D printing.
Overview of 3D Printed Material Strength
There are several desirable characteristics during 3D printing, one of which is material strength. There are different metrics for measuring the strength of a material, with tensile strength and impact toughness generally taken as the standards.
The tensile strength of a material is its resistance to breaking under tension. Furthermore, tensile strength is typically measured in megapascals (MPa). Aluminum has a tensile strength of between 40 and 700 MPa, while titanium has an average tensile strength between 240 and 1400 MPa.
Aside from tensile strength, impact toughness is another indicator of the mechanical strength of a material. Impact toughness (or impact strength) is the amount of energy a material can withstand during fracturing under impact.
Materials with high mechanical strength and strength-to-weight ratio are usually preferred in many industries. However, if a material is too strong, it may be challenging to use with 3D printing. Conversely, materials with weak mechanical strength are not rigid enough to use with 3D printing.
Influencing Factors on 3D Printed Material Strength
Different processing factors affect the material strength of a 3D printed material, and they include:
- Part orientation
- Infiltrant type
- Layer thickness
- Temperature
- Extrusion width
- Infill density
These factors are usually the ones assessed when trying to improve the strength of a particular 3D-printed material. Generally, the smaller the layer thickness or height, the better the quality of the 3D print. However, thinner materials are generally not as strong as thicker ones. Again, horizontal orientations are better for 3D printing.
How to Measure 3D Printed Material Strength
As several factors affect material strength, different tests must be carried out to correctly determine 3D printed material strength. Some of these tests are:
- Tension (puncture and stretching)
- Extrusion
- Compression
- Mucoadhesion
- Flexure
Challenges That Titanium and Aluminum Face in 3D Printing
Titanium and aluminum are two of the most used metals in many manufacturing industries today. However, they cannot be manufactured with 3D printing straightforwardly. Let’s consider why below.
Aluminum and 3D printing
Aluminum is one of the commonest metals on the planet today and has been used in manufacturing industries since the 1800s. The metal is lightweight, possessing a density of 2710km/m3, which justifies its use in many household products. Moreover, aluminum CNC is generally easy because the metal is moldable, with an elasticity modulus of around 70MPa.
However, aluminum metal alone is not strong enough to be used for metal 3D printing. For many industries to even consider the metal, it has to be alloyed with another suitable metal, like titanium. Also, aluminum metal is prone to cracking and tends to have inconsistent mechanical properties.
Titanium and 3D printing
Titanium metal, like aluminum, is also abundant today. The fact that titanium is corrosion-resistant, more temperature-durable, and lightweight has endeared it to many manufacturers. Over the last few years, the use of titanium has soared in the aerospace, defense, and medical industry.
Despite titanium’s accolades as an ideal manufacturing metal, it cannot be 3D machined because of the risk of fire and explosion hazards. This property has also been observed with finely divided aluminum properties.
How to Optimize Titanium and Aluminum for 3D printing
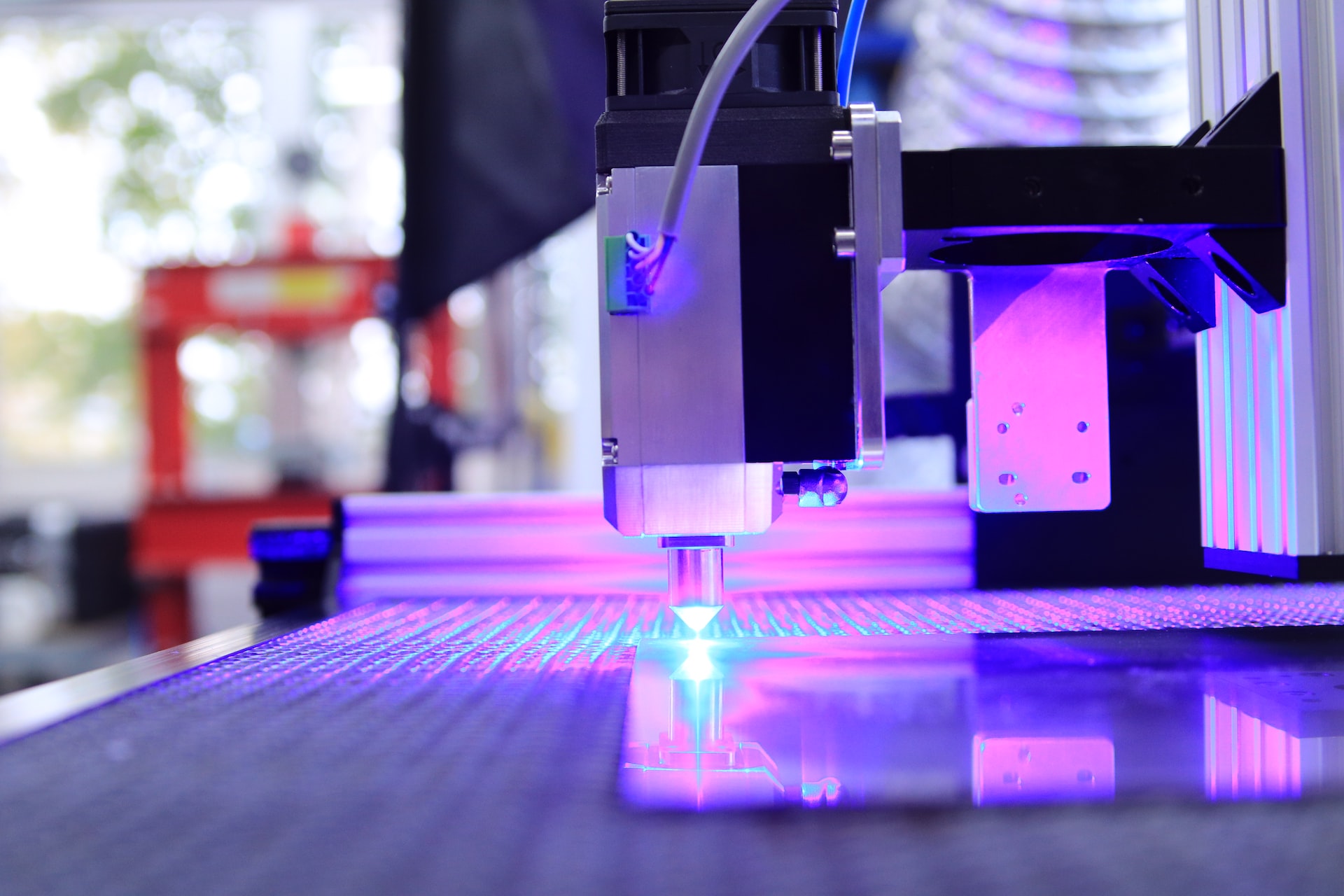
Photo by Opt Lasers on Unsplash
Aluminum is not strong enough for 3D printing. Titanium is also not suitable because of the fire hazard risks it poses. Manufacturers cannot effectively and safely use either of the two metals individually for 3D printing.
One solution that has caught the public eye is sintering branched surfaces on aluminum-matrix composites. This method was used by Russian scientists, with the lead researcher stating that the strength of Aluminium doubled when this method was employed.
This sintering method, done using the Selective Laser Melting (SLM) and Selective Laser Sintering (SLS) additive manufacturing techniques, was successful because of the surface of the metal. The team used nitrides and aluminum oxides, forming tiny layers between particles. These particles then attached to the metal matrix, making it twice as strong.
Another solution that has been explored recently is alloying both metals. The Titanium aluminide (TiAl) alloy is often used where lightweight and high strength/weight ratios are required. This alloy makes up for the individual weaknesses of both metals.
Conclusion
3D printed materials need to be strong. Many metrics can be of use in assessing material, with tensile strength and impact toughness being the commonest. While strength is a good property, balance is key so as not to impact the use of the metal in 3D printing adversely.
Aluminum and titanium are two of the most frequently used metals for manufacturing. However, because of the properties of these metals, they cannot be safely and effectively used for 3D printing. To combat this, Russian researchers have developed a technology that can double the strength of these metals for 3D printing. This new technology is still being tested, but it offers much-needed promise in 3D printing titanium and aluminum fields.